The Rise of Digital Twins in Manufacturing and Design
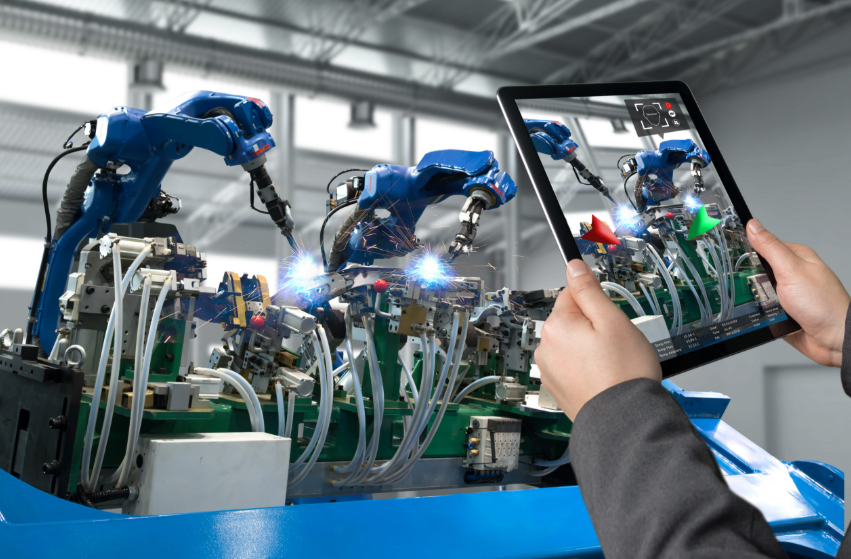
The emergence of digital twins is reshaping the landscape of manufacturing and design. This technology allows for the creation of accurate virtual replicas of physical assets. As a result, companies can enhance operational efficiency and foster innovation. By integrating these digital models with IoT and AI, the potential for predictive analytics grows. However, the implications of this shift extend beyond mere efficiency gains. The future of collaboration and design methodologies may hinge on these advancements.
Understanding Digital Twins: Definition and Functionality
Although the concept of digital twins has gained significant attention in recent years, their definition and functionality remain critical to understanding their impact on manufacturing and design.
Digital twins leverage virtual modeling to create real-time simulations of physical assets, enabling enhanced data synchronization. This approach allows manufacturers to optimize processes, predict failures, and innovate designs, ultimately fostering a more adaptive and efficient production environment.
See also: The Rise of Quantum Computing: A Game Changer in Technology
The Impact of Digital Twins on Manufacturing Efficiency
Digital twins revolutionize manufacturing efficiency by providing a comprehensive framework for real-time monitoring and analysis of production processes.
By utilizing predictive maintenance, manufacturers can identify potential equipment failures before they occur, minimizing downtime and optimizing resource allocation.
This data-driven approach enables companies to enhance productivity, reduce operational costs, and achieve greater flexibility, ultimately fostering a culture of innovation and continuous improvement in manufacturing environments.
Innovations in Design Driven by Digital Twin Technology
As organizations increasingly embrace digital twin technology, significant innovations in design processes emerge, reshaping traditional methodologies.
The use of virtual prototypes allows designers to iterate rapidly, while real-time simulations offer insights into performance under various conditions.
This paradigm shift not only enhances creativity but also empowers teams to make data-driven decisions, ultimately leading to more efficient and effective design solutions across industries.
Conclusion
As industries embrace the digital twin phenomenon, akin to Prometheus bestowing fire upon humanity, they unlock unprecedented potential for efficiency and innovation. This technology not only enhances manufacturing processes but also revolutionizes design methodologies, fostering a culture of rapid iteration and informed decision-making. The integration of digital twins with IoT and AI serves as a catalyst for predictive analytics and collaboration, illustrating a transformative shift that may redefine operational paradigms across sectors in the foreseeable future.